Боинг не торопится возобновлять поставки Дримлайнера – «лайнера мечты» Боинг-787 с композитным фюзеляжем и крылом. Официальная версия – устраняет «мелкие дефекты на каркасах самолетов». Почему это… ну такая себе отмазка? В общем, сегодня проведу краткий ликбез по композитам в авиастроении.
Корпорация Боинг не торопится возобновлять поставки своего самолета 787 Dreamliner, о чем нам совершенно открыто сообщает Блумберг. С июня американский аваистроительный гигант не передал заказчикам ни одного самолета, а в январе Боинг зафиксировал 5.5 миллиардов долларов издержек на производство модели 787, что не позволило получить прибыль от его продаж.
По сообщениям компании, она «устраняет мелкие дефекты на композитных деталях» самолетов. К тому же, целых 110 Дримлайнеров, находящихся в эксплуатации, потребовали весьма трудоемкого ремонта дверей. Когда речь идет о таком большом количестве самолетов – тут уже не спишешь на какие-то случайности или «доводку по месту». Проблема и в самом деле куда серьезнее.
Этот материал можно посмотреть на видео, там есть дополняющие иллюстрации - для лучшего понимания.
Боинг 787 стал первым большим магистральным самолетом, где были применены композиционные материалы именно в силовых частях конструкции, то есть в оболочке фюзеляжа и силовой части крыла. Композиты применяются в авиации уже несколько десятилетий, но в основном – для несиловых частей: разных обтекателей, законцовок крыла и все такое. Боинг стал первым, кто попробовал применить композиты для силовых частей. Но сейчас можно уже точно сказать, что вышло не очень.
Чтобы объяснить в чем же была ошибка Боинга мне придется провести небольшой ликбез по композитам в авиастроении.
Под композитом обычно понимают некий материал, состоящий из двух или нескольких компонентов. Тот, что наиболее активно применяется в авиации – это так называемый углепластик. (Да, стеклопластики тоже там есть, я в курсе. Но речь сейчас о силовых конструкциях - поэтому углепластики.)
Композит-углепластик состоит из двух компонентов: высокопрочного углеродного волокна и полимерного связующего. Это самое волокно представляет собой очень прочные углеродные нити. Чтобы сделать из этих нитей монолитную конструкцию их надо определенным образом положить слоями и чем-то скрепить. Скрепляют полимерным связующим или проще говоря – пластиком.
Можно было бы конечно залить чем покрепче – металлом, например. Но не получается с точки зрения химии, потому что между волокном и связующим должна образоваться прочная связь – адгезия. С этой точки зрения пластик подходит идеально. Но есть один ньюанс – с прочностью у пластика как-то не очень. А по сравнению с углеродным волокном – так вообще.
Но – пока речь идет о конструкциях, где запасы по прочности гигантские и вообще прочность это дело десятое – все очень даже отлично. Потому что композит почти в два раза легче стандартных авиационных сплавов. А вот когда конструкция должна работать на пределе возможностей – тут-то и вылезают проблемы. Пластик оказывается довольно хрупким и непрочным.
Значит ли это, что композиты нельзя применять в крыле и фюзеляже? Нет, не значит. Просто надо делать это с умом. То есть – с учетом преимуществ и недостатков этого самого композита.
А что же сделал Боинг? Он по сути взял за основу конструкцию металлического самолета и «заменил» металл на композит. То есть все части конструкции остались примерно те же: такая же тонкая обшивка и тонкостенные подкрепляющие элементы: стрингеры и шпангоуты. Они даже концепцию такой конструкции назвали Black Metal. То есть это как бы такой металл, только лучше. А слово Black здесь потому, что углепластик черного цвета.
Это конечно же было ошибкой. Причем концептуальной, то есть сам подход к тому как делать конструкцию оказался неправильным. Таких примеров в истории человечества, кстати, огромная масса.
Вот например, испокон веков люди строили дома и другие строения из дерева. А что такое типовая деревянная конструкция? Это когда ставишь два деревянных бревна - цилиндра и сверху – третий, в качестве перекрытия. А потом где-то в Древней Греции люди решили строить дома из камня. А что, камень же прочнее, правда? И стали делать свои здания с колоннами. Два каменных цилиндра и сверху перекрытие. То есть тупо скопировали «деревянную» концепцию.
Но такие конструкции из камня оказались не очень. Ведь дело в том, что камень очень прочный на сжатие, но плоховат на растяжение. А когда кладешь его на перекрытие – он изгибает под собственным весом и в нижней части образуется зона растяжения. Ну и сразу трещина, конечно. В итоге до наших дней греческие здания если и сохранились, то в неважном состоянии.
А вот римляне – те оказались более прошаренными. Они учли особенности камней и стали делать арки и своды, в которых все камни только сжимаются, а не растягиваются. И римские здания сохранились гораздо лучше.
Точно так же с любым конструкционным материалом. Если меняешь материал – приходится изобретать совершенно новую конструкцию, на новых принципах. Иначе – провал. Как и вышло в итоге у Боинга.
В авиации тип материала меняется уже не в первый раз. На заре пионерской авиации самолеты строили, как известно, из деревянных брусков, из которых делали рамы и стягивали металлическими тросами. А из брусков – потому, что это естественный элемент, который можно сделать из дерева.
Потом, когда свойств дерева перестало хватать для более высоких скоростей и грузоподъемностей – решили переходить на металл. Кстати, первые металлические самолеты – такие как советский «Сталь-2», очень напоминали деревянные. Те же самые рамы, только металлические.
Но вскоре из металла научились делать тонкие листы, упрочненные с помощью проката. И тогда конструкция тоже поменялась – появилась знакомая всем нам «труба с крыльями». То есть естественный элемент конструкции из металла – это лист. Из него можно сделать обшивку и тонкостенные стрингеры, которые можно к этой самой обшивке приклепать.
А что же композит? А композит – это прежде всего нить. Не брусок, как у дерева. И не лист, как у металла. А нить, жгут или лента, что сути не меняет. А что хорошего и прочного можно сделать из нитей? Особенно с учетом того, что скреплять их приходится слабым и хрупким пластиком. Это вопрос пока открытый, хотя и здесь есть кое-какие классные разработки. Но об этом в другой раз.
Так что проблемы Боинга с его Дримлайнером по моему скромному мнению еще только начинаются. А нам главное – делать правильные выводы и не повторять чужие ошибки.
Комментарии
Просрали полимеры (с)
Ага, только не мы))
Врёте Вы всё: посмотрите на количество докторских диссертаций американских ВУЗов по пидорасологии. Это небывалый прогресс! революция в науке.
Там была война отраслевых стандартов настолько жёсткая что на первой или первых машинах был полный криминал - утечка топливо в крыло. Баки создали согласно требованиям для металлических а вставили в пластиковые, где они успешно разгерметизировались ввиду более активного поведения пластиковового крыла на потоке. На самолёётах это слегка видно а вот на планерах выгибается до 30градусов конец. Несколько меньше на высотных дронах.
Чтобы как-то оно не поломалось при влёте как сие много раз было ещё с металлических конструкций того же МакКриди (Инженер с большой буквы, первый мускулолёт перелетевший Ла Манш) делают вот такой колхоз:

Также те же первые Зефиры запускала толпа наземной команды явно до того порядком потренировавшись для набора скорости - высотные машины имеют малу скорость взлёта т.к. на высотах обычно килограммы на м2 всего, когда эскизно прикидывал свой на 40км там 2,5-3,5кг получалось, в зависимости от источника энергии и движителя, не на бензине же...
Эрбас не умеет работать с композитами на дронах:
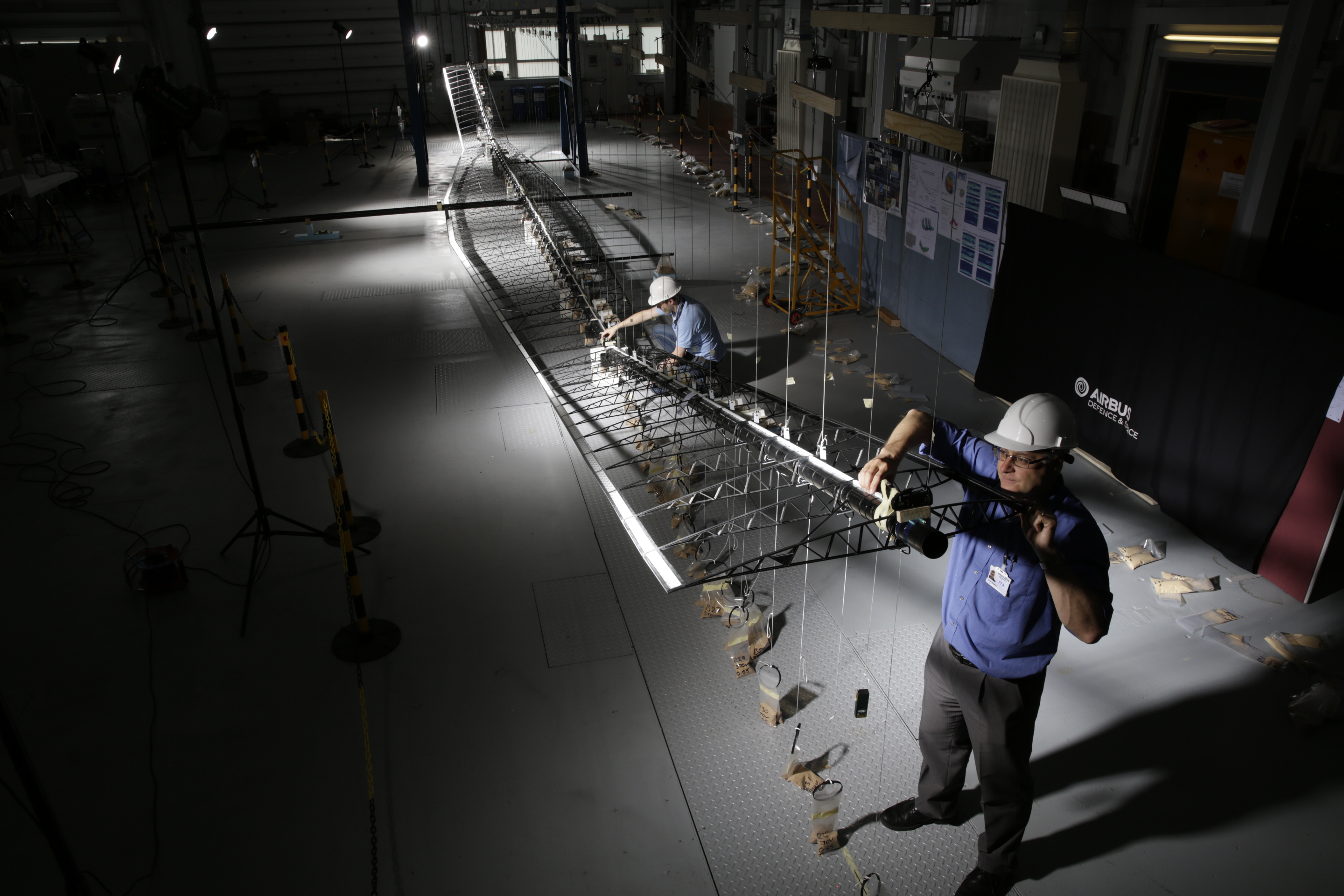
Хорошо видно что они делают как если бы имели дело с каким металлом лишь немного изменяя крыло. Quinetiq для передней корки применяли 6-угольными сотами упрочнение/делали более жёстким, я лично в 2012 это делал выдавливанием исходного композита когда он вспучивался под определённым воздействием (с). Т.е. в отличие от англичан у меня получалась с одной стороны гладкая с другой сотовая поверхности корки крыла, арамид-арамидный композит с НЕПРЕРЫВНЫМИ волокнами применявшегося нетканого материала, так прочнее. И Кроме того в своём композите добивался сворачивания в одном и расправлен с возможностью застыть в другом состоянии крыла, т.е. при подъёме шаром или сбросе на 15+км с самолёта он раскрывался как бабочка. Наиболее реалистичным был вариант с шаром, т.к. несколько минут минимум требовалось.
Наиболее интересные с точки зрения конструкции из тех что в США и Англии делали имели не привычный набор везде а часто ВЯЗКУ жгутами волокон Помимо улучшенной работы - на растяжение достигалась нужная жёсткость конструкции, шла распределение нагрузок много лучше чем при привычных для моделистов и дроноведов методов - вообще авиаспециалистам не занимавшихся дронами неведомым. Вместе с тем, при определённых волокнах и связующем это позволит выдержать резкие потоки на границах слоёв, там разница ветров 100м/с может быть всего на сотнях метров.
Спасибо за развернутый комментарий.
А есть же супер прочные пластики - высокомолекулярные полимеры.
Есть, но с углеродным волокном их совместить не получается.
Это с чего бы ... пултрузией да - не совместите термопласт ... но существуют ещё и экструзионные технологии как бы ..
Экструзия рукопожатна, но сами пластики — увы, нет (в рассматриваемой области).
И главное тут — их рабочая температура.
Больно диапазон узкий.
да все там совмещается. главное- обработать поверхность волокна серной кислотой. чтобы хвостов на нее навешать кислотных, которые дадут адгезию к матрице. ну не кислотой- так электролизом осадить на поверхность че-нить, оксид графена там намутить на ней, или каких-нибудь атомов меди прицепить. долго, дорого и глупо, но технологии есть. не в этом проблема, проблема в неоднородных условиях реального нагружения таких деталей. вся эта композятина хорошо держит каждая свой тип нагрузки, кто-то растяжение, кто-то сжатие, кто-то сдвиг, кто-то трибологию хорошую имеет (скользкий или к трению устойчивый), но держит только что-то свое. А как начнешь что реальное делать- то выяснится, что вот тут мы жмем, тут тянем, а тут- трется и греется. и обязательно где-то что-то не вывозит. а уж есть встанет вопрос ремонта- то ваще, композиты эти неремонтно пригодны никак, только полная крупноузловая замена.
Композиты в детали только через ТММ и сопромат ... поддерживаю - ремонтопригодность никакая, только замена ... композит работает дольше металлов в критических условиях если условия предполагают именно его, композита, физ-мех ...
Два мудреца, я гляжу, потрогали слона за
хухобот. Сделали свои выводы?Композит можно сделать сколь-угодно хорошим. А остальной самолёт Вы к нему гвоздями прибъёте? Приварите? Назовите хотя бы 17 способов неразъёмного соединения композита без спускания всех его рабочих качеств в унитаз.
Стесняюсь, но спрошу - а почему 17?
И, если Вы знаете, то не проще ли не изображать И23, а сразу написать и мысль (посыл, теорему), и обоснование, и выводы
А почему бы и нет? Если Вам станет на порядок легче, назовите 16. Или 15.5.
Вроде как это очевидно любому человеку: композит есть совмещение разнородных материалов, собственно тем он и полезен. Но именно это и создаёт проблему его присоединения к другим конструкциям без ухудшения его свойств.
Вот Вы, к примеру, бурите напряжённую бетонную балку? Анкера в неё садите? Думаю, все понятен исход такой самодеятельности.
И тут возникает большой вопрос: зачем нужна композитная структура, если равнопрочно соединить её ни с чем не получается? Ради моды? Слово красивое? А может быть, надо сразу делать одну гигантскую деталь?
С Вами всё вроде понятно.
Одну деталь делать не надо. Это нельзя ремонтировать.и контролировать.
Вот так новость! С Су-47 поэтому и закончили играться. Всё было красиво, прочно и легко. Но вот ведь незадача - одна дырка и всей конструкции хана.
Потому, вроде бы, браться за дело стоило бы с другого конца.
а мы болтами его прикручиваем. делаем дырку (для тех, кто понимает), волокно укладываем аккурат кругом возле этой дырки, а в дырку- болтяру на 24. и держит. вполне себе сносно держит.
Так можно и гвоздями, только чаще. Тоже держать будет.
Дырку, извиняюсь, между волокнами делаете, небось? Или нарушаете целостность волоконной структуры?
А теперь простой вопрос: каков расход массы на обеспечение избытка прочности для сверления, на крепёжные элементы? Достигается ли при этом равнопрочность всей конструкции?
Вы невнимательны. Мы дырку делаем в модели, в компьютерной. А волокна выкладываем вокруг этой дырки уже в процессе печати реального элемента. Мы прекрасно понимаем, что нарушение целостности волоконной структуры- это смерть для изделия и допускать такого нельзя ни при каком раскладе, и не допускаем. Какое сверление? Вы об чем? Тут вон vs пишет, что кобальтовые сверла об углепластик приземляет за 10-15 проходов, а у нас финансирования на кобальтовые сверла в таких количествах не выделяют, нам только на расходники для печати и немножко- на волокно дают.
Как изъяснились, так и получите. Я видал массу умников, которые непринуждённо сверлят/бурят армированные конструкции, а потом удивляются, что что-то пошло не так. А потом убеждённо называют материал говном.
На вопросы с прочностью, избыточной массой, ну и, до кучи, с распределением напряжений в соединяемых деталях, Вы естественно, но красноречиво, помалкиваете.
Попробуйте гвозди, их тоже можно меж волокон))
почему помалкиваю- я же прямо говорю- волокна вдоль максимальных растягивающих напряжений! главные оси тензора напряжений под заданную нагрузку довольно неплохо определяются любым КЭ-пакетом.
Конечно, легко. Так воспользуйтесь этой лёгкостью, оцените лишнюю массу шва для получения равнопрочной конструкции.
Вот этот персонаж у меня отмечен как копия ВладиславаЛ, если что. Ну вы и по семантике это должны были понять.
А в мелких карбон лучше,лучше чинится ,такие как велосипед .
косметически он только чинится. восстанавливается внешний вид, а прочностные свойства- нет. волокна порваны- все, прочность кончилась. Матрица, опять же, эпоксидка поверх эпоксидки красиво прилипает и выглядит, как будто ничего не было, но вот граница раздела старой и новой смолы- имеет очень неочень адгезию, и нагрузку держит очень плохо- ослаблена раз в десть получается. и получается, что внешне вроде все починили, а вот по свойствам- оно безвозвратно ослаблено. или менять целиком, или никаких других вариантов.
Аэрокомпозит уже на термопластах не одну собаку съел, но пока очень тяжко идёт
А как делают композитные стеклопластиковые корпуса, лодок, яхт, кароблей минных тральщиков
В матрицу выкладывается стекломатериал, могут наполнитель добавлять типа сот, пробки ,ПВХ или ещё чего, закрывают герметично пленкой, дают вакуум и начинают смолу закачивать с отвердителем. Вакуум тянет смолу через стекло, пропитывая. Потом все это полимеризуется. А, перед этим, гелькоут наносится на матрицу. После снятия это будет лицевая сторона. Гелькоут определяет цвет изделия,ну и это защитный слой для изделия. От воды, уф в зависимости от марки . как то так
Называется метод вакуумная инфузия
Почему таким методом корпус самолёта сделать нельзя ? Или подобным
Почему таким методом корпус самолёта сделать нельзя ? Или подобным
Почему таким методом корпус самолёта сделать нельзя ? Или подобным
Потому что этот метод с очень большим трудом обеспечивает необходимую пористость и на деталях ограниченных размеров. Потому что это далеко не самый экономичный способ как по используемым материалам, так и производительности. Да и по физико-механическим свойствам. Есть еще целый ряд причин
Если мы говорим о том о чем пишет ТС конечно
В то же время есть виды и типы изделий которые можоно получить только той же вакуумной инфузией, вернее не так- самым экономичным будет именно этот метод да и опять же ФМС
да всё проще. "эпоксидка" тяжелее "авиационного металла" при одинаковой прочности :-)
да и применение "смолы" - литьевое. а металла - листовое. первое - для всевозможных форм (дизайн), второе - конструкция (модель)
вам самолёты какие? красивые? или летающие? :-)
Разговор то про композиты а не про эпоксидку
Почему нельзя? Делают - например корпуса кораблей в десятки метров длинной. Самый большой - это тральщик, (не магнитный) корпус которого, кстати, рассчитан на близкий подрыв морской (! до тонны ВВ!!) мины. Длинна - ~70 метров... Самое дорогое тут - термокамера для отверждения соответствующего размера.
а какую нагрузку должен выдерживать стеклопластиковый корпус лодок, яхт и кароблей? Я хочу сделать дома параболическу тарелку (реальный кейс :-), ну и что мне делать? штамповать ее из люминя? не реализуемо. А вот взять пенопласту, сделать шаблон из фанеры по линейке, и из этого пенопласта по этому шаблону за день наждаком нашлифовать круглый параболик- нет проблем. Потом намазать его парафином, обложить стеклотканью и залить смолой- еще два часа возни. и потом еще шкурануть изнутри получившийся тазик. Сложная криволинейная поверхность с хорошей точностью сделана в домашних условиях из композитного суперматериала. не, просто из композитного говна. но зато сложная криволинейная поверхность с хорошей точностью. Вот поэтому и делают корпуса яхт и лодок из стеклопластика- потому что технологично из него обводы обшивки выводить. Но это штучная узкоспециализированная работа (ручная, кстати).
Минные тральщики- отдельная песня. им нужна магнитная прозрачность, чтоб мины их не чувствовали, и коррозионная стойкость- соленая вода мало кому нравится. им приходится быть пластиковыми, а тут без вариантов- только пластик с волокном. Качество низкое, нормальный металлический корпус был бы гораздо приятнее, но условия эксплуатации обязывают, а титан- ну совсем дорого в таких объемах. приходится есть кактус.
пултризуя говно работающее как раз против технологии прочности углепластика.
увидите углепластик сделанный пултрузией - бегите от него как черт от ладана.
Например профили?))
Вы куда то не в ту степь
Тут есть нюанс. Они, как правило, очень не любят низкие температуры. И ещё, довольно неплохи на удар, а вот на изгиб уже не очень.
>> И ещё, довольно неплохи на удар, а вот на изгиб уже не очень.
на изгиб 14мм углепластиковая труба с толщиной стенки 1мм изгибается на 10см в под нагрузкой в 50кг. Я самолично измерял.
Дюраль под такой нагрузкой сломается, сталь согнется.
Сколько у меня падало БПЛА с разных высот, алюминий гнет и рвет в хлам, карбон еще ни разу не сломался за 7 лет.
Ну мой комментарий относился к вещам типа пвд, к примеру корты хоккейные из него делают.
Я сам в теме стеклопластиков 20 лет, последние 12 свое производство.
Небось на Instron "измеряли", да? Bluehill какой версии был? Так, чисто интересуюсь)))
Углепластики плохо держат удар Стекло или арамид намного лучше
Вам нужно чтобы углепластик гнулся?) Если нет то его жесткость намного выше чем у металла
Нету.
Пластики это хорошо, это кошерно, но есть масса нюанцов…
Короче, без титаниума пока никак.
карбоновый пластик в разы прочнее титана
А поливинилиденфторид химически устойчивее нержи и обладает выдающейся гладкостью.
Нельзя сравнивать по одному параметру.
и нахрена эта "химическая устойчивость" самолету?
Вы собираетесь летать в облаках серной кислоты?
Это просто возражение.
Повторюсь: нельзя хвататься за один параметр. Всё надо в комплексе считать.
Полагаю, вы и сами это прекрасно знаете.
вот именно.
поэтому ваш один параметр "химическая стойкость" в топку - он нафиг не сдался в конструкционной авиации.
Естественно.
Вы с начала гляньте: я ровно про это и говорю. Для чего и привёл совершенно абсурдный пример.
P.S. Вот как раз в пластиках неплохо разбираюсь.
Страницы